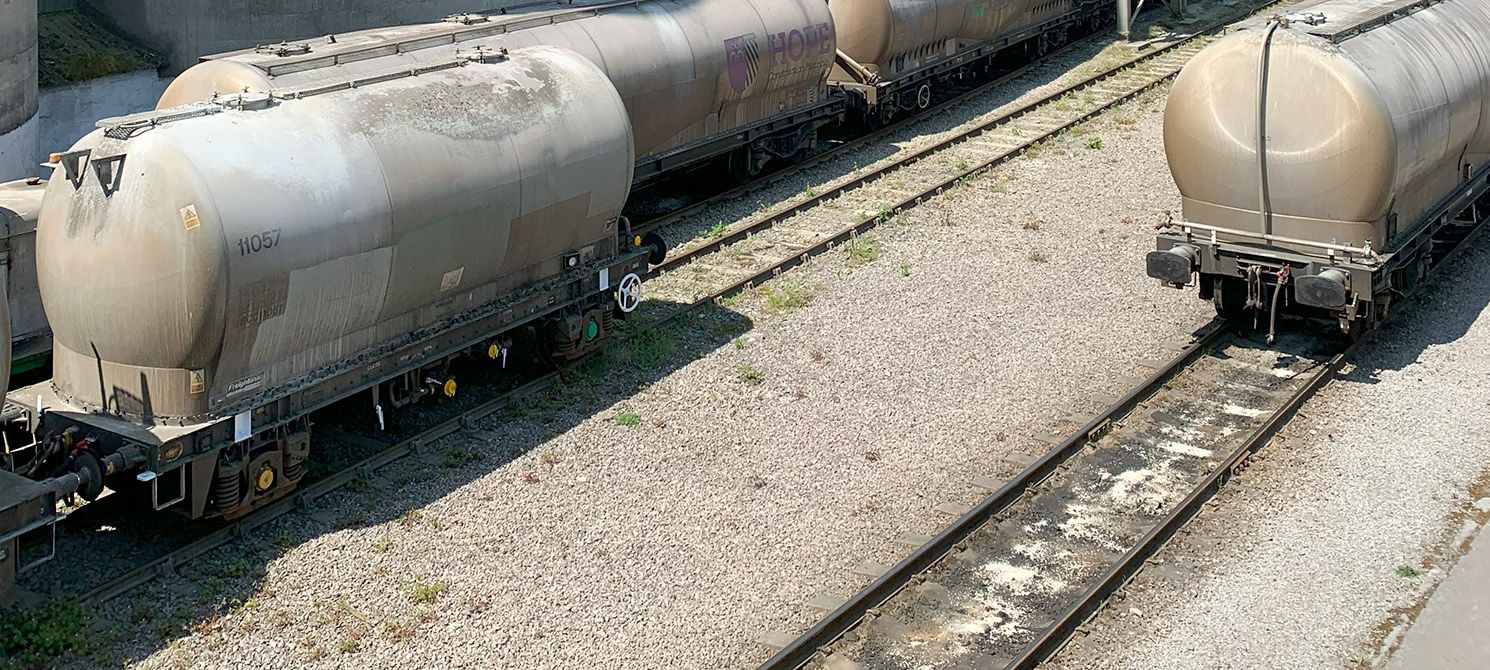
Breedon Group PLC
Breedon Group PLC Achieves 95% Maintenance Efficiency by Modernising with Green Custard on AWS
Overview
UK-based construction materials supplier Breedon worked with AWS Partner Green Custard to modernise its material tracking processes within its UK cement business. Historically reliant on paper records and spreadsheets, the company faced inefficiencies in tracking materials and managing costs.
Green Custard replaced outdated systems with a cloud-connected platform powered by Amazon Web Services (AWS). Equipped with modernised infrastructure, Breedon gained real-time insights into its rail logistics operations, achieving 100% data capture compared to 60% on previous paper-based systems. This has helped the company reduce operational waste and allowed colleagues to focus on higher-value tasks, keeping Breedon on track for continued innovation.
The Challenge
Breedon supplies construction materials across Great Britain, Ireland, and the USA, and has typically relied on manual, paper-based systems for operations. This approach, inherited from successive acquisitions and mergers, hindered consistency and efficiency. While paper-based processes had been effective, they were increasingly out of sync with the needs of modern supply chain logistics.
Accurate tracking—of rail wagons carrying cement-based products, in this case—is critical to Breedon’s vertically integrated business model. However, legacy infrastructure and processes introduced gaps in data that made it difficult to monitor logistics at a granular level, resulting in only 60% of data being successfully captured. Without the ability to analyse trends or identify inefficiencies, issues persisted. For example, Breedon knew that material carryback—meaning cement not properly unloaded from wagons—was a significant challenge. Without real-time data monitoring, it was impossible to grasp the full scale or increased operational costs.
Paper records risked being lost or damaged, and employees had to manually transfer handwritten data into spreadsheets—a time-consuming process prone to error. Breedon lacked real-time visibility into supply chain movements without a centralised digital system. “We knew there were problems with our historical processes,” said Tim Copping, head of operational technology at Breedon. “So we focused our efforts on identifying a new solution."
Breedon sought to enhance visibility, improve accuracy, and uncover actionable insights to optimise its operations. The gaps in its legacy system also presented an opportunity to align historical workflows and fully modernise logistics management.
“[Breedon Group] now has information and intelligence that were never available to us before; this has allowed us to visualise data and make informed solutions about how we manage supply chain logistics going forward.”
- Tim Copping, Head of Operational Technology, Breedon Group
The Solution
To address these challenges, Breedon partnered with Green Custard. An AWS IoT Competency Partner, Green Custard aimed to replace outdated logistics processes with a digital platform that offered greater efficiency and visibility on AWS.
“The technology portfolio that AWS has in place for IoT solutions is fantastic,” said James Green, director of Green Custard. “It’s very broad, very comprehensive, so it makes our life simpler when we can leverage those building blocks rather than reinventing the wheel.”
Breedon was using legacy infrastructure not designed to connect to the cloud, so Green Custard deployed an edge device, utilizing AWS IoT Greengrass to link this infrastructure to AWS and AWS IoT Core for seamless data ingestion. This data is then securely stored in Amazon DynamoDB, where it can be accessed and analysed by the Breedon team.
While the Green Custard solution unified disparate environments, it made additional challenges more apparent. “We thought at first it was just about weights and wagons,” said Copping. “But once we got into the details, it became clear we needed a more nuanced solution for the complexities of our operations.”
For example, the process of loading and dispatching wagons varied significantly between transport hubs, which made timing and logistics management less predictable. To address this, Green Custard and Breedon developed a custom “train builder” feature that provides logistics teams with the flexibility to digitally manage wagon configurations, addressing discrepancies in loading and dispatch while maintaining data accuracy.
The Results
By transitioning from paper processes to a modern, cloud-connected system, Breedon has achieved a 100% success rate for data capture. With thousands of rail wagons now tracked digitally in real-time, Breedon has a complete record of material movements across its rail supply chain—a paperless paper trail. This accuracy has eliminated the challenges of missing or unreliable data for a clearer view of operations.
In addition, the introduction of real-time monitoring has enabled Breedon to address inefficiencies like material carryback more effectively. Wagons that return with residual cement are now able to be identified quickly and repaired. This approach to maintenance has already reduced the frequency of carryback incidents and improved the performance of targeted wagons by 95%.
The solution has also saved Breedon teams over 250 hours of time spent on manual input annually. Rail-wagon loading information is now more readily visible and available, which allows Breedon teams to spend more time on higher-value tasks.
By addressing its legacy challenges and embracing digital tools, Breedon has set the stage for continued innovation. Now, Breedon is beginning to use AI-powered reporting, predictive maintenance, and deeper integrations with logistics and order management systems to unlock even greater efficiencies. The system’s scalable architecture provides opportunities to incorporate advanced technologies and further automation, ensuring that Breedon remains competitive—and on track—long into the future.